در بخش اول مقاله، قالبگیری بادی (دمشی) و انواع فرآیندهای آن معرفی شد. قالبگیری دمشی عبارت بود از شکلدهی به روده مذاب پلاستیکی که در قالب قرار گرفته، با دمیدن هوا در آن و با سه روش اکستروژن، تزریقی و تزریقی کششی انجام میشد. در بخش دوم مقاله، نخست پلاستیکهایی که برای این نوع قالبگیری مناسب هستند و در ادامه مزایا و معایب قالبگیری بادی (دمشی) را بررسی میکنیم.
انتخاب پلاستیک مناسب برای فرآیند قالبگیری بادی
یک پلاستیک چه ویژگیهایی باید داشته باشد تا برای این نوع قالبگیری مناسب باشد؟
برای پاسخ به این سؤال، در ابتدا لازم است با دو مفهوم ترموپلاستیک و ترموست آشنا شویم. پلیمرها براساس نوع رفتارشان در برابر حرارت، به دو دسته ترموپلاستیک و ترموست تقسیم میشوند. ترموپلاستیکها یا گرمانرمها گونهای هستند که بر اثر حرارت، نرم و ذوب شده و در صورت سرد شدن میتوانند دوباره به حالت جامد برگردند (این کار را میتوان بارها انجام داد). اما در ترموستها یا گرماسختها بر اثر حرارت، واکنش شیمیایی رخ میدهد که سبب میشود بین زنجیرهای پلیمری، اتصالات عرضی (cross-links) برقرار و ماده سفت شده، قابلیت ذوب شدن و در نتیجه فرآیندپذیری خود را از دست بدهد. بر همین اساس است که در فرآیندهای شکلدهی پلاستیکها از ترموپلاستیکها استفاده میشود. فرآیندهایی چون قالبگیری بادی، قالبگیری تزریقی، قالبگیری فشاری و …. . بهعنوان مثال نایلون، پلیکربنات، پلیاتیلن، پلیپروپیلن و پلیبوتیلن، ترموپلاستیک و اپوکسی، پلیایمید و آلکیدها، ترموست هستند.

در بین خانواده بزرگ ترموپلاستیکها، پلیالفینها بهسبب ویژگیهایشان، در انواع فرآیندهای شکلدهی از جمله قالبگیری تزریقی، اکستروژن ورق، اکستروژن پوششی و بهطور خاص در قالبگیری دمشی استفاده میشوند. مزیت رزینهای پلیالفینی شامل فرآیندپذیری، چقرمگی و مقاومت شیمیایی خوب، وزن سبک و قیمت نسبتاً ارزانتر از سایر پلاستیکها هستند. علاوهبر این، خواص پایه پلیالفینها را میتوان به طیف گستردهای از خواص مورد نظر تبدیل کرد. این مواد میتوانند بههمراه پلیمرهای گوناگون دیگری اکسترود شوند. برای مثال، اتیلن وینیل الکل (EVOH) و نایلون، برای تولید ظروف چند لایه با خاصیت مانع نفوذ گازها استفاده میشود. پلیالفینهایی که در قالبگیری بادی کاربرد دارند، عبارت از LDPE ،LLDPE ،MDPE ،HDPE، اتیلن کوپلیمر مانند اتیلن وینیل استات (EVA)، پلیپروپیلن و پروپیلن کوپلیمر هستند. [2]
حوزه عمده کاربرد پلیالفینها در فرآیند قالبگیری دمشی، به شرح زیر است:
- بستهبندی محصولات غذایی، مواد شوینده، مواد آرایشی و مراقبت شخصی
- قطعههای وسایل نقلیه مانند تانک سوخت، بطری روغن، مجاری هوا و پشتی صندلی
- محصولات مصرفی، مانند اسباببازیها، لوازم خانگی و کالاهای ورزشی

در ادامه پاسخ به این پرسش، مفهوم گرید را بررسی میکنیم.
گرید (Grade)
پلاستیکها بسته به نوع کاربرد، براساس گرید، تقسیمبندی میشوند. در واقع گرید نشان میدهد یک پلاستیک چه خواصی دارد و برای چه کاربردی مناسب است. برای نمونه، در جدول 2 تفاوت خواص و کاربرد چند گرید از پلیاتیلن دیده میشود.
جدول 1- تفاوت خواص و کاربرد چند گرید از پلیاتیلن سنگین [2]
گرید | خواص | کاربرد |
BL3 | دانسیته و سفتی بالا، ESCR خوب | قالبگیری دمشی بطریها، ظروف تا سقف 5 لیتر، بستهبندی اقلام دارویی و سورفکتانت |
I4 | بسیار راحت جاری میشود، دانسیته، سختی و سفتی بالا | تزریق لوازم سبک وزن خانگی، قطعات یک بار مصرف، قطعات پیچیده |
EX3 | چقرمگی خوب، نقطه ژل پایین، استحکام پارگی خوب، سفتی و چسبندگی خوب، جرم مولکولی بالا | فیلمها و ورقهای بسته بندی |
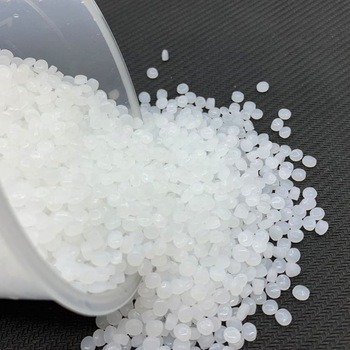
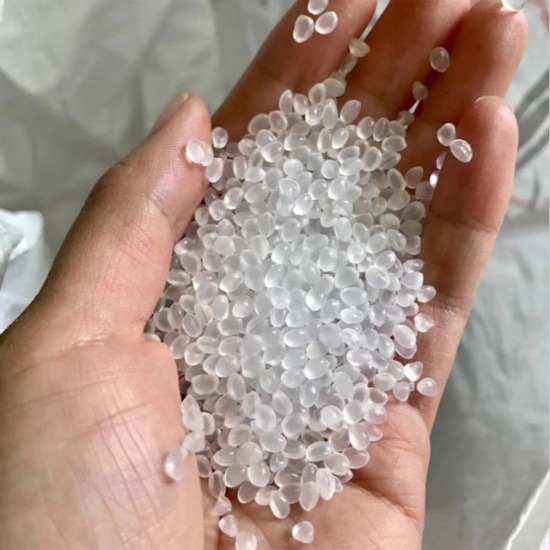
همچنین در دو جدول زیر نیز خواص فیزیکی و مکانیکی چند گرید از پلیاتیلن سنگین و پلیپروپیلن آورده شده است.
جدول 2– خواص فیزیکی و مکانیکی گریدهای مختلف پلیاتیلن سنگین [2]
ISO | 1183 | 1133 | 179/1eA | 527 | 868 | |
گرید | فرآیند | دانسیته (KJ/m2) | (MFI (190°C/5kg و (gr/10min) | استحکام ضربه (KJ/m2) | تنش تسلیم (MPa) | سختی (Shore D) |
BL2 | قالبگیری دمشی | 0/944 | 1/1 | 11 | 22 | 60 |
EX3 | لوله | 0/948 | 0/22 | 25 | 23 | 62 |
I4 | تزریق | 0/954 | 4 | 3 | 26 | 62 |
EX4 | فیلم | 0/956 | 0/28 | – | 27 | 60 |
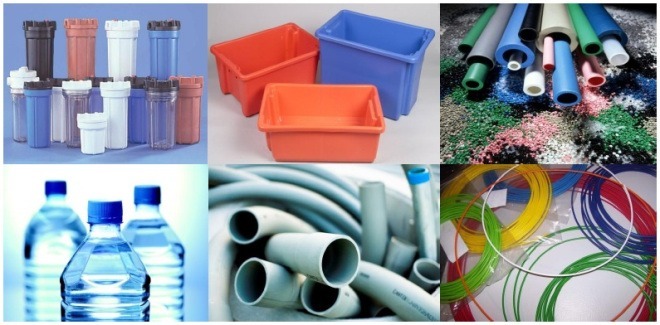
جدول 3– خواص فیزیکی و مکانیکی گریدهای مختلف پلیپروپیلن [3]
ASTM | D1238 | D256 | D790 | D638 | |
گرید | فرآیند | (MFI (230°C/2.16kg و (gr/10min) | استحکام ضربه ایزود شکافدار (J/m) | مدول خمشی (MPa) | کرنش تسلیم (%) |
HP432C | قالبگیری دمشی | 0/3 | 200 | 1350 | 34 |
RP344R | قالبگیری دمشی | 25 | 55 | 1100 | 10 |
HP500P | تزریق | 17 | 30 | 1550 | 12 |
HA701T | تزریق | 45 | 28 | 2050 | 6 |
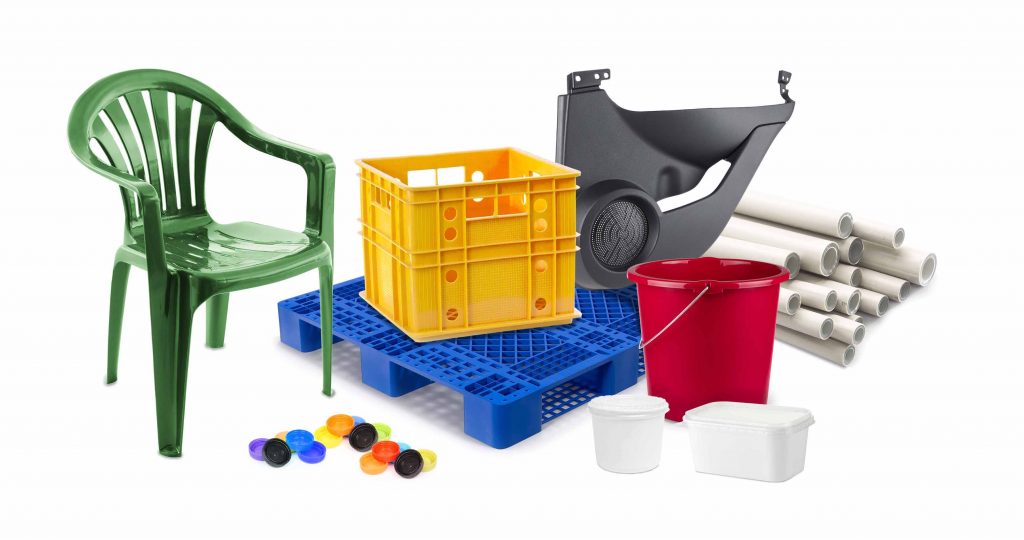
همانگونه که در جدولهای بالا مشخص است، برای فرآیند شکلدهی پلاستیکها از گریدهای مختلف استفاده میشود.
مزایا و معایب قالبگیری بادی
قالبگیری بادی مانند روشهای دیگر شکلدهی پلاستیکها، مزایا و معایب خاص خود را دارد که بهصورت گذرا در مقاله قبل به برخی از آنها اشاره شد. در جدول زیر، این مهم بهطور کاملتری بررسی شده است.
جدول 4– مزایا و معایب فرآیندهای قالبگیری دمشی [1]
فرآیند | مزایا | معایب |
اکستروژن | ابزارآلات ارزانتر (30-40%) | بهرهوری پایین |
اکستروژن | سرعت تولید بالا | ضایعات زیاد (40-5%)، بهویژه در ظروف با حجم کم |
اکستروژن | امکان تولید ظروف با دسته توخالی و دهانه گشاد | احتمال وجود خطوط حدیده یا اکسترودر در محصول |
اکستروژن | قابلیت اکسترود کردن همزمان چند ماده | محصول نیاز به پلیسهگیری دارد |
اکستروژن | قابلیت کنترل وزن؛ ایدهآل برای نمونهسازی | احتمال رخ دادن پدیده “تورم حدیده” |
تزریقی و تزریقی کششی | بهرهوری بالا (93-98%) | ابزارآلات گرانتر |
تزریقی و تزریقی کششی | ضایعات کمتر از یک درصد | محدودیت در تولید ظروف با حجم زیاد |
تزریقی و تزریقی کششی | کنترل بهتر ضخامت دیواره قطعه | محدودیت در تولید ظروف با دهانه گشاد |
تزریقی و تزریقی کششی | نیاز به پلیسهگیری ندارد | تولیدکننده کنترل کامل بر پروفایل دما ندارد |
منابع
[1]. Samuel L.Belcher, practical guide to injection blow molding, CRC publication, 2007
[2]. http://v1.petrochem-ir.net/en/product/polymers?page=hdpe.htm
[3]. http://www.jppc.ir
گرد آورنده: حمیدرضا طیاری